FR4 is the most common grade dielectric material that is used in the fabrication of circuit boards. This material is incorporated in single-sided, double-sided, and multi-layered boards.
Here are a few qualities of FR4 materials that make them popular:
- Wide range of operating temperature (50°C to 115°C)
- Higher Tg value (about 180°C)
- Offers decent mechanical properties to maintain board structure integrity
- Cost friendly when compared to other materials
What does FR4 stand for?
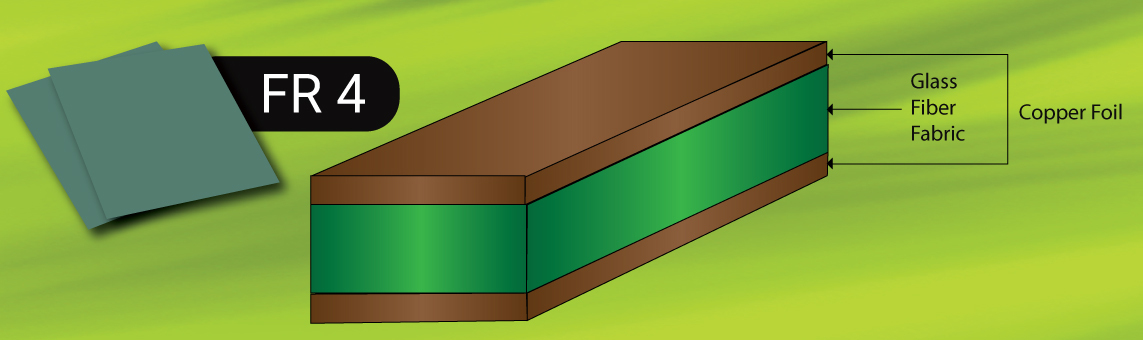
FR stands for flame retardant, and the number ‘4′ indicates woven glass-reinforced epoxy resin. The characteristics of FR4 vary significantly depending on the manufacturer, although it is commonly known for its mechanical strength and water resistance. This material performs as an insulator in PCBs by isolating adjacent copper planes while also providing overall mechanical strength.
What are the properties of FR4 substrate?
Flame retardant
Chemicals that are applied to materials to prevent or delay the spread of fire are known as flame retardants. FR4 substrates have excellent thermal, mechanical, and electrical properties making them a perfect choice for a wide range of electronic applications. Flame retardant laminates and prepregs are extremely versatile, adaptable to a variety of manufacturing procedures, and produce predictable results.
Good electrical properties
The electrical properties of a PCB material are critical for signal integrity and impedance considerations. They specify how fast an electrical signal propagates through the material and how much electrical charge it can retain in a given volume. The table below lists a few important electrical properties along with their typical values.
Electrical property | Typical value |
---|---|
Dielectric constant (Dk) | 5 at 1MHz |
Electrical strength | 800 to 1800volts/mil |
Dissipation factor (Df) | 0.009 at 1MHz |
Surface resistivity (ρS) (Ohm/square unit) | 105 to 1010 |
The given values can vary depending on the manufacturer. For example, FR4 has a dielectric constant that varies between 3.8 and 4.8 depending on the glass weaving style, thickness, and resin content.
Low moisture absorption
Moisture absorption is the ability of a PCB material to resist water absorption when immersed in water. It is given by a percentage increase in the weight of a circuit board material due to water absorption under controlled conditions. FR4 materials offer a low moisture absorption of 0.10% when immersed in water for 24 hours.
Limitations of FR4 circuit board materials
FR4 has been used in the production of printed circuit boards for many years now. It’s inexpensive and provides adequate electrical insulation. However, when FR4 is used in high-speed applications the following problems may occur:
Insulating stability
Although FR4 is a great insulator, it has its limits when subjected to high power, voltage, or heat. If certain limits are exceeded, the materials’ insulating properties will deteriorate, and they will begin to conduct electricity instead. This causes circuit board failures.
Controlled impedance
FR4 does not offer uniform dielectric constant like high-speed board materials. As the frequency goes up the Dk varies. Dielectric constant tolerances for high-speed materials are less than 2%, whereas for FR4 it is up to 10%. Dk variations in FR4 impose challenges while maintaining impedance values. Hence, this material is not a preferred choice for controlled impedance boards.
Signal losses
Signal loss is an important aspect of PCB design, particularly in high-frequency applications. FR4 isn’t the best material for these applications since it has a greater Df (dissipation factor) than high-frequency materials.
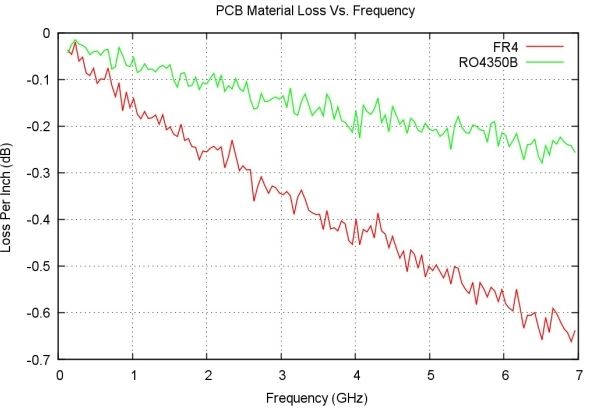
FR4 has a Df of around 0.020, while most high-frequency laminates have a Df of around 0.004, which is a fourth of FR4’s Df. The smaller the Df, the lesser is the overall signal loss. One more drawback is that the Df of FR4 increases as the frequency of a signal increases. As a result, these PCBs suffer higher signal losses than a board built using a high-frequency laminate. The graph above plots frequency vs. loss per inch (dB) of FR4 and Rogers RO4350B (high-speed material). It clearly depicts that the FR4 material suffers a greater loss at high frequencies.
Temperature stability
FR4 materials are not recommended for devices that are exposed to high temperatures. Also, these materials do not support lead-free soldering, this is because reflow temperatures for no-lead PCB assembly can reach up to 250 °C. This is significantly higher than the Tg of many FR4 versions.